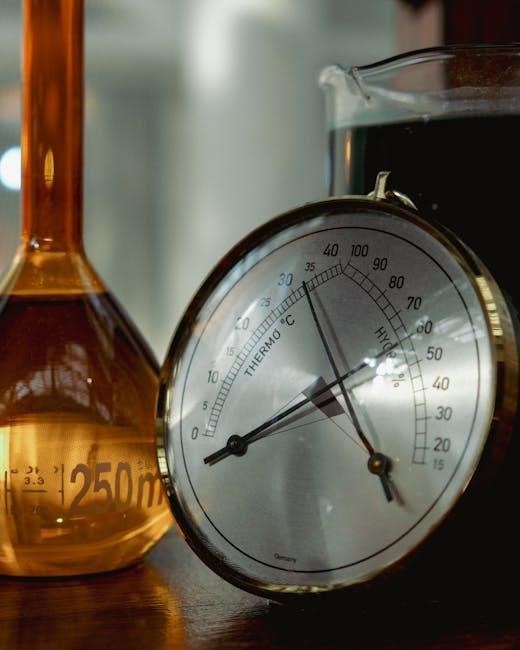
Système de Freinage Pneumatique Poids Lourd: Guide Complet
Welcome! This comprehensive guide explores the intricate world of heavy-duty air brake systems․ From fundamental principles to advanced troubleshooting, we delve into every aspect․ Safety, maintenance, and operational efficiency are key․ This resource is designed for technicians and drivers alike, ensuring a thorough understanding․
The air brake system is fundamental to the safe operation of heavy vehicles․ Unlike hydraulic brakes in smaller vehicles, air brakes use compressed air to apply braking force․ This system is essential for managing the substantial weight and momentum of trucks, buses, and trailers․ Air brake systems offer superior stopping power and reliability when properly maintained․
Understanding the components and their functions is crucial for drivers and technicians․ The system relies on a constant supply of compressed air, generated by an air compressor and stored in reservoirs․ When the driver presses the brake pedal, air is released from the reservoirs to the brake chambers, activating the brakes․
Safety is paramount with air brake systems․ Regular inspections and maintenance are vital to ensure optimal performance․ Air leaks, worn components, and improper adjustments can compromise the system’s effectiveness․ Proper training and certification are necessary for anyone operating or maintaining vehicles equipped with air brakes․ Knowing the system’s intricacies ensures safety․
Composants Principaux du Système
The air brake system consists of several key components working in harmony․ The air compressor, driven by the engine, supplies compressed air to the system․ Reservoirs store the compressed air, ensuring an adequate supply for braking․ The brake pedal valve controls the release of air to the brake chambers, dictating braking force․
Brake chambers convert air pressure into mechanical force, pushing the brake shoes against the drum or disc․ Air lines and hoses connect these components, transmitting compressed air throughout the system․ A governor regulates the air pressure, maintaining it within a safe operating range․ Safety valves prevent over-pressurization, protecting the system from damage․
Other critical components include the slack adjusters, which maintain proper brake shoe clearance․ Quick release valves improve brake response time, especially in longer vehicles․ Antilock braking systems (ABS) enhance stability during hard braking․ Understanding each component’s role is crucial for effective maintenance and troubleshooting․ These parts together enable safe and reliable stopping․
Compresseur d’air
The air compressor is the heart of the pneumatic braking system, responsible for generating the compressed air necessary for operation․ Typically driven by the vehicle’s engine, it draws in atmospheric air, compresses it, and delivers it to the air reservoirs․ The compressor’s capacity is crucial; it must supply sufficient air to maintain adequate pressure during frequent braking․
Efficient operation is essential to prevent overheating and premature wear․ Many compressors incorporate a cooling system, often utilizing engine coolant or an integrated air-cooling mechanism․ Regular maintenance, including filter checks and lubrication, extends the compressor’s lifespan․ A malfunctioning compressor can lead to insufficient air pressure, compromising braking performance and safety․
Modern air compressors often feature sophisticated designs, incorporating features like automatic unloader valves․ These valves regulate the compressor’s output, preventing over-pressurization of the air reservoirs․ Proper functioning of the compressor ensures a reliable and consistent air supply, vital for the overall effectiveness and safety of the heavy vehicle’s braking system․
Réservoirs d’air
Air reservoirs, also known as air tanks, are crucial components in a heavy vehicle’s pneumatic braking system․ They serve as storage vessels for the compressed air generated by the air compressor․ These reservoirs ensure a consistent and readily available supply of air for braking and other auxiliary functions, like air suspension․
Typically, a heavy vehicle will have multiple air reservoirs strategically located throughout the chassis․ This distribution optimizes air delivery to the brake chambers and other pneumatic devices․ The reservoirs are designed to withstand high pressures and are equipped with safety valves to prevent over-pressurization․ Regular draining of moisture and contaminants from the reservoirs is essential to prevent corrosion and system malfunctions․
The size and number of air reservoirs are determined by the vehicle’s braking requirements and air consumption demands․ Proper maintenance, including regular inspections for leaks and corrosion, is vital for the reliable operation of the air brake system․ A loss of air pressure due to leaking or damaged reservoirs can significantly impair braking performance, posing a serious safety hazard․
Soupape de commande au pied
The foot valve, also known as the brake pedal valve or treadle valve, is the driver’s primary control for activating the air brake system in a heavy vehicle․ This valve regulates the amount of compressed air delivered from the reservoirs to the brake chambers, controlling the braking force applied to the wheels․ The position of the foot valve directly corresponds to the desired braking intensity․
When the driver presses the brake pedal, the foot valve opens, allowing compressed air to flow to the brake chambers․ The further the pedal is depressed, the greater the air pressure delivered, resulting in stronger braking․ Releasing the pedal closes the valve, exhausting air from the brake chambers and releasing the brakes․ The foot valve is designed for precise control, allowing the driver to modulate braking force for smooth and safe stops․
Proper functioning of the foot valve is critical for effective braking․ A malfunctioning valve can lead to delayed braking response, uneven braking, or even complete brake failure․ Regular inspection and maintenance of the foot valve are essential to ensure its reliability․ Any signs of leakage, stiffness, or erratic operation should be promptly addressed to maintain optimal braking performance․
Cylindres de frein
Brake cylinders, also known as brake actuators or air chambers, are crucial components in an air brake system․ Their primary function is to convert the energy of compressed air into mechanical force, which is then used to apply the brakes․ Typically found at each wheel, these cylinders receive pressurized air from the control valve and translate it into a linear motion․
Inside the brake cylinder, a diaphragm or piston is pushed by the incoming air, moving a pushrod․ This pushrod, in turn, actuates the brake mechanism, such as a slack adjuster in drum brakes or a caliper in disc brakes․ The force exerted by the cylinder is directly proportional to the air pressure applied, allowing for controlled and modulated braking․
Different types of brake cylinders exist, including service brake cylinders, spring brake cylinders (for parking and emergency braking), and combination cylinders․ Regular inspection of brake cylinders is vital․ Technicians should check for leaks, damage, and proper operation of the pushrod․ A malfunctioning brake cylinder can significantly reduce braking performance and compromise safety․ Proper maintenance and timely replacement are essential for reliable braking․
Fonctionnement du Système de Freinage Pneumatique
The operation of an air brake system in heavy vehicles relies on the principles of compressed air to deliver braking force․ It begins with the air compressor, which draws in atmospheric air and compresses it, storing it in air reservoirs․ These reservoirs act as a reserve of pressurized air, ready for use when braking is required․
When the driver presses the brake pedal, the foot valve controls the release of compressed air from the reservoirs․ This air travels through brake lines to the brake chambers located at each wheel․ Inside the brake chambers, the air pressure pushes against a diaphragm, which in turn moves a pushrod․
The pushrod actuates the brake mechanism, engaging the brake shoes against the brake drum or the brake pads against the rotor․ This creates friction, slowing down or stopping the vehicle․ Releasing the brake pedal exhausts the air from the brake chambers, disengaging the brakes․ The entire process is carefully regulated to provide consistent and controlled braking performance, crucial for the safe operation of heavy vehicles․
Freinage de service
The service braking system, also known as the primary braking system, is the standard braking mechanism activated each time the driver presses the brake pedal during normal driving conditions․ This system is designed for routine speed reduction and stopping maneuvers․ When the driver applies pressure to the brake pedal, it signals the air brake system to release compressed air from the reservoirs․
This compressed air flows through brake lines to the brake chambers at each wheel․ Inside the brake chambers, the air pressure acts upon a diaphragm, which in turn moves a pushrod connected to the brake mechanism․ The movement of the pushrod forces the brake shoes against the brake drum or the brake pads against the rotor, generating friction․
The friction slows down or stops the rotation of the wheels, bringing the vehicle to a controlled halt․ The amount of braking force applied is directly proportional to the pressure exerted on the brake pedal, giving the driver precise control over the vehicle’s deceleration․ Upon releasing the brake pedal, the air pressure in the brake chambers is released, disengaging the brakes and allowing the wheels to rotate freely once again․
Freinage d’urgence
The emergency braking system in heavy vehicles serves as a vital safety net in critical situations․ Unlike the service brake, which is used for routine stops, the emergency brake is designed for situations where the service brake fails or is insufficient to prevent an accident․ This system utilizes a separate mechanism, often employing spring brakes, to provide a powerful stopping force․
Spring brakes are held in the released position by air pressure․ In an emergency, a loss of air pressure, either intentional or due to a system failure, causes the springs to apply the brakes forcefully․ This mechanical application of the brakes ensures that the vehicle can be brought to a stop even without a functioning air system․ Emergency braking can be activated manually by the driver using a control valve or automatically in response to a critical drop in air pressure․
It’s crucial to remember that emergency braking is not intended for regular use․ It’s for dire situations only․ Frequent use can damage the system and compromise its effectiveness when truly needed․ Regular inspections are essential to ensure the emergency brake is functioning correctly․
Maintenance et Sécurité
Maintaining the air brake system on a heavy vehicle is paramount for safety and operational efficiency․ Regular maintenance prevents failures, ensuring the system functions reliably when needed most․ Neglecting maintenance can lead to brake fade, reduced stopping power, and even complete system failure, posing significant risks on the road․ A proactive approach is crucial․
Safety starts with thorough inspections․ Before each trip, drivers should check air pressure gauges, listen for leaks, and ensure brake components are in good condition․ Regularly scheduled maintenance, performed by qualified technicians, should include inspecting air lines, reservoirs, and brake chambers․ These checks should also include adjusting the brakes, lubricating moving parts, and replacing worn components․
Proper training is also vital for both drivers and maintenance personnel․ Understanding the system’s operation and potential issues allows for early detection of problems․ Drivers need to know how to recognize warning signs, such as unusual noises or vibrations, and how to respond appropriately․ Keeping detailed maintenance records helps track the system’s performance and identify recurring problems․
Contrôles réguliers
Regular inspections are the cornerstone of a safe and reliable air brake system․ These checks are essential to identify potential problems before they escalate into costly repairs or, worse, accidents․ A comprehensive inspection should be conducted at regular intervals, typically before each trip and during scheduled maintenance․ Drivers play a crucial role in these inspections․
Before each trip, drivers should perform a walk-around inspection, paying close attention to the air brake system․ This includes checking air pressure gauges to ensure they are within the proper operating range․ Listen carefully for any air leaks around hoses, fittings, and brake chambers․ Inspect brake lines for cracks, kinks, or damage․ Verify that brake shoes or pads have sufficient lining thickness․
During scheduled maintenance, qualified technicians should conduct a more thorough inspection․ This includes examining the compressor, reservoirs, and control valves․ Check for proper function and signs of wear or corrosion․ Adjust brakes as needed to maintain optimal performance․ Replace any worn or damaged components promptly․ Detailed records of these inspections should be maintained․
Dépannage courant
Even with regular maintenance, air brake systems can experience problems․ Knowing how to troubleshoot common issues can save time and prevent more serious damage․ Air leaks are among the most frequent problems․ Listen carefully for hissing sounds, particularly around fittings and hoses․ Use soapy water to pinpoint the exact location of the leak and replace the affected component․
Low air pressure can indicate a problem with the compressor, governor, or air lines․ Check the compressor belt for proper tension and condition․ Ensure the governor is functioning correctly and maintaining the correct pressure range․ Inspect air lines for kinks, cracks, or obstructions that could restrict airflow․ A faulty pressure protection valve can also cause low air pressure․
Uneven braking can be caused by several factors, including worn brake shoes or pads, malfunctioning brake chambers, or improperly adjusted brakes․ Inspect brake linings for wear and replace them as needed․ Check brake chambers for leaks or damage․ Adjust brakes to ensure they are properly balanced․ Addressing these issues promptly will maintain optimal braking performance․
Formation et Certification
Operating and maintaining heavy vehicles with air brake systems requires specialized knowledge․ Proper training is crucial for ensuring safety and compliance․ Many institutions and organizations offer comprehensive air brake training programs․ These programs typically cover the theory of air brake systems, component identification, inspection procedures, and troubleshooting techniques; Hands-on experience is also essential for developing practical skills․
Certification demonstrates a driver’s or technician’s competence in working with air brake systems․ Certification programs often involve written and practical exams․ Passing these exams indicates that the individual has met the required standards of knowledge and skill․ Certification can enhance career opportunities and improve credibility․ Staying up-to-date with the latest technologies and regulations is important for maintaining certification․
Continuing education is also important for those working with air brake systems․ New technologies and regulations are constantly being introduced․ Participating in refresher courses and workshops can help drivers and technicians stay informed and maintain their skills․ Investing in training and certification is a worthwhile investment in safety and professionalism․